来源:哈尔滨工业大学 作者:王书铭 王广林 李云峰 邵东向 陶崇德
摘要:介绍7一种新型电液伺服阀精密弹性元件智能化刚度测量技术。针对生产现场中使用的手动测量法的不足,提出一种新的刚度自动测量方法。采用计算机驱动步迸电机,步进电机作为控制执行器对精密弹性元件快速而又连续的施加载荷,实现自动加载;力和位移信号送到计算机进行处理和计算。理论分析和测试结果表明,该方法可以有效的解决精密弹性元件刚度测量中的测量精度低、操作复杂、效率低等问题,对精密弹性元件能够高效的完成刚度测量,得到刚度曲线,并且不重复性测量误差低于1%。
关键词:智能测量刚度测量仪
1.引言
在航大、航海、航守领域常用的控制器件电液伺服阀中,广泛的麻用r精密弹性元件(二立要指衔铁组件)作为力敏感元件以获得反馈信号。衔铁组件的刚度特。P}:对电液伺服阀的性能影响很大,赢接关系到控制精度和灵敏度等性能指标。l蚓此,在设计l:对其刚度值要求极其严格,然而在加Ttp保让能够达到设计要求的刚度值是通过:一测量一再加1.一再测量的反复过程来实现的,所以刚度值的测晕技术对衔铁组件的制造起到了决定。m竹作用,在衔铁组件加工过程中对其刚度的大小要求极其严格。而随着现代制造技术的发展,衔铁组件的加工精度和加工效率要求越来越高,㈨此需要对检测其刚度值的测量仪器在测量精度和测量效率上提出更高的要求与之相匹配。}1前生产现场中l:要使用两种方法测量精密弹性儿件的变形特性。一是传统的手动测量方法,即:加载砝码,用线纹尺或光学仪器测量位移量,人r计算获得刚度值,其最大的缺陷是:测量精度差,__I==作效率低,人工劳动强度大;:是半自动测量,即手工操作机构对被测试件施加载荷,传感器获得力和位移信号,信号经处理后由单片机系统采集并处理计算出刚度值,其缺陷是:仍然没有完全把人工从测量r{,解放出来,并目+只能测试有限的个别点的刚度,不能完全反映零件完整的刚度特性。
本文提出一种自动测量精密弹性元件刚度特性的新方法,自动加载,实现多点测量并使用最小二乘法拟合出精密弹性元件的刚度f}}I线,并可获得很高的测量精度。
2.自动测量系统的测量原理
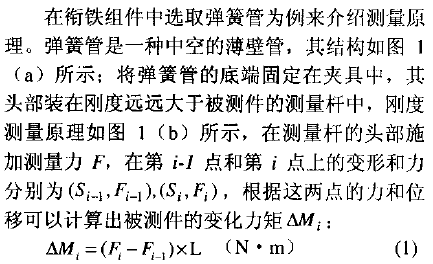
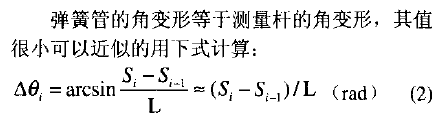
上式中L为测量杆的中心距,即力臂的长度。
选取n点进行测量并用最小二乘法处理测量数据,得到力矩一转角刚度的计算公式如下:

3.自动测量系统的设计
自动测量系统的组成框图如图2所示,自动测量系统主要是由三部分组成的,安装被测试件、传感器、步进电机和微动机构的测量台架部分;完成步进电机驱动、传感器信号处理、模/数转换及隔离的接口电路部分;控制整个测量系统进行测量并进行数据处理、计算及结果输出的计算机控制系统。
图2自动测量系统组成
3. 1测量台架
作为被测试件和传感器的载体,测量台架主要部分的结构简图如图3所示。图中微动机构将步进电机的大角位移进给转换成微量角位移迸给,而千分螺丝的作用是将角位移进给转换成直线微位移并且推动弹性块向上产生微小变形,固定在弹性块上的力传感器在这个微小变形的作用F平行上移,通过铁芯衔持板对被测原件施加测量力,完成自动加载功能。力传感器既作为测力元件又作为施力元件,避免了由于施力和测力分别实现而带来的误差。电感测微仪的线圈部分固定在台架上,铁芯安装于铁芯衔持板上随力传感器一起运动,铁芯与线圈之间互不干涉。位移传感器通过测量铁芯衔持板的位移实现对被测元件的变形量进行非接触式的测量,避免了因存在附加测量力而造成的载荷测量误差。
3. 2接口电路
接口电路主要包括将传感器采集的力和位移信号进行放大等处理的二次仪表电路、将放大后的模拟信号转换为数字信号的A/D转换电路以及驱动步进电机运转的步进电机驱动电路。
3.3计算机控制系统
计算机控制系统主要包括四部分。将转换后的数字信号送到计算机的数字量输入接口卡;实现环形分配器控制步进电机来完成自动加载的数字量输出接口板;控制核心的计算机;输出测量结果和刚度曲线的彩色喷墨打印机。计算机系统的主要功能是控制测量系统进行测量,进行数据的处理、计算及测量结果的输出。自动测量系统的上位机软件是采用vc++6.0设计的,具有良好人机交互功能。测量主界面如图4所示。
4.主要技术指标
位移变形检测:
力检测:
刚度测量:
最大测量范围700 μm
分辨率O.1 μm
精度±0.5 μm/100μm
±2μm/全范围
最大测量范围9810mN
分辨率lmN
精度±0.1%
精度±o.7%
5.结论
本文所介绍的电液伺服阀精密弹性元件智能化刚度测量仪,是由计算机控制、采样分析,可实现自动加载、测量及输出功能,提高了测量和加工的效率;保证测量的不重复性误差低于1%,并可获得刚度曲线为精密弹性元件的设计提供参考。
此外,还可以通过设计不同的夹具对其它精密弹性元件的刚度值进行测量。
|