来源:广西科技大学鹿山学院 作者:耿雪霄 刘志英 陆桂岐 覃淑萍 蔡李同兴
[size=10.9091px]摘要:通过对汽车发动机气缸盖导管孔的加工中MAPAL单刃枪铰刀在应用中存在导管孔直线度差、气门插不进的问题进行调研,并通过15。精加工部分刃口和750粗加工部分刃口分别进行受力分析、再钝化处理并进行生产实践检验对比。最后发现MAPAL单刃枪铰刀进行150精加工部分刃口钝化处理后,气门插不进的问题有所改善,但导管孔直线度差的问题没有改善;进行750粗加工部分刃口钝化处理后,基本没有出现“上小下大”等气门弯曲情况发生,加工效果有了明显改善。
[size=10.9091px]
[size=10.9091px] 关键词:导管孔;直线度;气门;钝化处理
[size=10.9091px]
[size=10.9091px] 0、引言
[size=10.9091px]
[size=10.9091px] 发动机作为汽车的核心部件,发动机气缸盖的加工质量好坏则是实现发动机高性能的基础,特别是气缸盖气门座圈(阀座)和导管孔的加工精度的好坏将直接影响发动机的性能,因此行业对阀座工作锥面与导管孔的跳动、导管内孔与外圆的跳动规定了严格的公差:气缸盖阀座锥面跳动≤0.03~0.04 mm,导管内孔对外圆的跳动≤0.15~0.20 mm⋯。
[size=10.9091px]
[size=10.9091px] 长久以来,阀座锥面和气缸盖导管孔加工一直是气缸盖加工的技术难题,在批量生产中,关注加工工艺优化、加工方式、定位方式、切削刀具材料及其结构形式等都是稳定地保证公差的有效途径。目前世界上主流的刀具主要是MAPAL提供的座圈导管复合式枪铰刀,本文以MAPAL枪铰刀为例,主要研究单刃导管孔加工刀具在国内某汽车公司气缸盖加工导管孔时出现导管孔直线度差、气门插不进问题,并通过枪铰刀的150精加工部分刃口和75。粗加工部分刃口分别进行受力分析、再通过钝化处理并进行生产实践检验对比,发现75 o粗加工部分刃口钝化处理后,基本避免出现“上小下大”等气门弯曲情况发生,加工效果有了明显改善;150精加工部分刃口钝化处理仅仅改善了气门插不进的问题,但对解决导管直线度差的问题无任何作用。
[size=10.9091px]
[size=10.9091px] 1、发动机导管孔的加工工艺分析
[size=10.9091px]
[size=10.9091px] 国内某汽车公司发动机制造工厂引进德国先进的气缸盖自动化生产线,生产设备全部为五轴联动数控机床,其生产的B10和B12发动机气缸盖的气门座圈和导管均为粉末冶金压制烧结而成,具有较高的硬度和耐磨性,从表1工艺技术要求可以看出,产品气门座圈锥面和导管孔相对尺寸及表面精度要求非常高,且由于其加工材质相对较硬,可见实际生产过程中气门座圈和导管孔的加工较为困难。
[size=10.9091px] 表1座圈和导管加工工艺要求
[size=10.9091px] 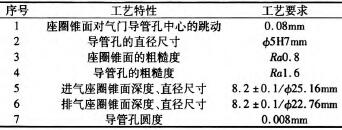
[size=10.9091px] 从工艺上分析,座圈导管加工难度较大,导管孔孔径小且深,属于深孔加工[21。加工刀具悬伸长,刚性不足,对刀具要求非常高。加工座圈和导管刀具的配备选用目前世界上主流的德国MAPAL公司的刚性复合刀具,可在一次进刀完成座圈和导管的加工‘3 3(见图1)。
[size=10.9091px]
[size=10.9091px] 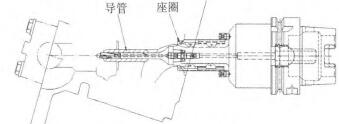
[size=10.9091px] 图1座圈导管加工情况
[size=10.9091px]
[size=10.9091px] 刀具的设计原理是利用支承导条来吸收切削产生的振动和阻力,类似普通车床的跟刀架,避免加工中产生“让刀”造成导管孔中心线相对座圈跳动超差。导管加工部分采用精密研磨的PCD刀片,铰刀杆上镶有两块PCD导条,在刀片进入导管约0.2mm之后,PCD导条也进入到已加工导管的表面起到支撑作用,并吸收切削所引起的振动,从而保证加工内孔的圆度和圆柱度。PCD导条在切削过程中还起到挤压修光作用,使工件表面更光滑。该加工工艺由两步组成:①用弘.90mm双刃引导刀对导管孔进行预加工,类似于做一个钻套,保证后续刀具位置度;②用单刃PCD铰刀和座圈镗刀一次成形M J。
[size=10.9091px]
[size=10.9091px] 2、MAPAL刀具在加工导管孔中出现的问题
[size=10.9091px]
[size=10.9091px] 自正式投产以来,装配线常发现有气缸盖有个别导管孔气门插不进,造成气缸盖无法进行装配现象,平均每个月约出现20件,数量多的每个月达到40件,严重影响生产效率,员工抱怨较大。个别缸盖气门稍用力能插入完成装配,但装配后气门运动不畅,则发动机有可能发生气门卡死,引发安全事故。图2就是售后反馈发动机抖动有异响,拆解后发现的气门撞伤活塞问题。
[size=10.9091px]
[size=10.9091px] 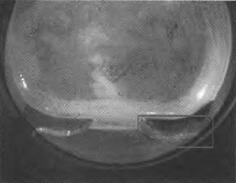
[size=10.9091px] 图2气门撞伤活塞问题
[size=10.9091px]
[size=10.9091px] 为查清问题所在,解决安全隐患,对配气系统零件气门和导管孔展开了调查。首先对气门进行了随机抽样检测,抽检发现所有气门尺寸均符合图纸公差,可排除气门问题。
[size=10.9091px]
[size=10.9091px] 再重点关注导管孔加工过程中产生的问题。将售后和装配退回的多个问题零件拆解后拿回生产线测量导管孔直径发现,同一个零件上并不是所有导管孔都发生撞活塞或者气门运动不畅情况,一般只有1—2个孔存在该问题。线旁检具测量问题孔时发现导管孑L存在上截面小下截面大的情况,合格孔孔径均为上截面大下截面小。
[size=10.9091px]
[size=10.9091px] 为什么测量会出现这样的差异呢?气缸盖生产线精加工工位SPC检测站导管检具采用无锡爱锡量仪有限公司的气动检具,测量点为离孔口大约3~4mm的上下两个截面(见图3),气动量仪利用了这样一个物理原理:流量与压力都与间隙的大小成比例关系,同时压力和流量相互之间成反比例关系。导管气动量仪是当要测量的导管孑L壁与测头喷嘴间隙越小时反馈读数越小,反之越大。正常能插进气门孔测量一般都是上截面测量数值大于下截面测量数值,或上下截面数值相差不多的情形[5]。
[size=10.9091px]
[size=10.9091px] 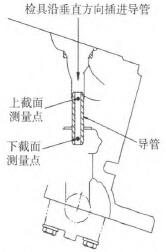
[size=10.9091px]
[size=10.9091px] 图3气缸盖生产线精加工工位SPC检测站导管检具
[size=10.9091px] 当出现气门插不进时,测量气门插不进孔的孔径值多数情况下读数为上截面数值比下截面数值小,即“上小下大”情况,但同一个缸盖中的8个导管孔不是每个孑L都出现气门插不进现象,只是其中的一个或者两个孔出现异常,且发生气门插不进工件不是连续出现,而是间断出现,因此过程质量监控困难。线上操作员工为避免出现批量报废事故,只能增加工件抽检频次,另外测量时一旦发现“上小下大”的情形随即换刀,造成换刀辅助时间的增多,影响生产产量,操作员工劳动强度大。
[size=10.9091px]
[size=10.9091px] 3、问题分析及改进方案
[size=10.9091px]
[size=10.9091px] 3.1原因分析
[size=10.9091px]
[size=10.9091px] 将出现“上小下大”且气门插不进的导管孑L用三坐标测量导管孑L内壁的真实形状,发现其不是真正意义的上截面直径小下截面直径大,而是导管孔下端出现弯曲,即导管孔直线度不好,如图4所示。
[size=10.9091px]
[size=10.9091px] 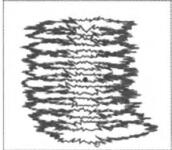
[size=10.9091px]
[size=10.9091px] 图4导管孔下端的弯曲现象
[size=10.9091px]
[size=10.9091px] 气动检具是根据测量喷嘴孔与孑L壁之间的间隙的变化反馈孔径尺寸,如果导管孔出口端(下截面)产生弯曲变形,测量喷嘴孔与孔壁之间的间隙也会随之变大,气检反馈其读数偏大,而上截面直线度好,与孔壁间隙不变,测量读数正常,即出现“上小下大”情形(见图5)。直线度超差严重时,导管检具会在下端面和导管孔壁接触无法转动,通常出现这样的情形气门也无法顺利通过导管。
[size=10.9091px]
[size=10.9091px] 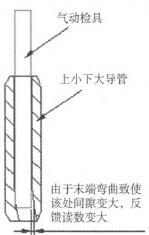
[size=10.9091px] 图5“上小下大”情形
[size=10.9091px]
[size=10.9091px] 为了查清导管孔加工弯曲的原因,对气缸盖导管孔加工刀具进行分析。气缸盖导管采用MAPAL单刃复合刀具加工,刀具采用可换刀片式结构,不但可以节约刀具加工成本,且刀具直径可以通过调节机构控制,调节方便快捷,较适合大批量生产中使用。通常将导管PCD刀片预设寿命为1200件,一旦到达寿命后则强制更换新刀片。统计发现导管刀片更换新刃口时较容易出现“上小下大”情况,这类刀具如果上下截面孔径值相差不是很大,不做任何处理将该刀重新放到机床使用后“上小下大”情况消失,经长期使用跟踪发现,当导管刀片到达一定寿命后基本不出现上小下大气门插不进情况,表2是统计2011年1月至5月出现“上小下大”次数和对应的寿命区间。
[size=10.9091px] 表2“上小下大”次数和对应的寿命区间表
[size=10.9091px] 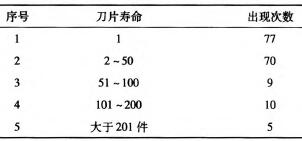
[size=10.9091px] 从数据可以看出:
[size=10.9091px]
[size=10.9091px] 2011年1月至5月,导管刀具共出现“上小下大”171次,其中:新刀片首件所占的比例为45%,总寿命低于100件(包括首件)所占的比例为:86%,刀片总寿命高于100件时所占的比例为:8.8%。
[size=10.9091px]
[size=10.9091px] 新刀片前50件出现“上小下大”次数较多,而在加工了100件之后基本没有再出现“上小下大“问题。从该现象分析应该是新刀片刃口过于锋利,切削轻快,径向力小,当毛坯硬度不均或者其他原因导致导条轻微脱离已加工表面,导条失去引导作用,导致导管孔直线度差,严重的气门无法插入。而加工了100件以后刃口已有一定程度的磨钝,其径向力增加,使得PCD导条能够与已加工表面贴合更加良好,发挥导条的引导作用,保证导管孔的直线度(见图6)。综合以上分析,增大新刀片的切削力,保证导条良好贴合,可以解决该问题。
[size=10.9091px]
[size=10.9091px]
[size=10.9091px] 图6加工过程中的受力分析
[size=10.9091px]
[size=10.9091px] 3.2精加工刃口钝化处理
[size=10.9091px]
[size=10.9091px] 增大新刀片的切削力,可以通过刃口钝化来实现。MAPAL导管加工刀片刃口部分可划分为3部分,75。部分为粗加工采用和引导刀一样的形式,去除大部分余量,15。偏角部分为精加工,修光刃为零度偏角,对已加工表面进一步修光,如图7所示。
[size=10.9091px]
[size=10.9091px] 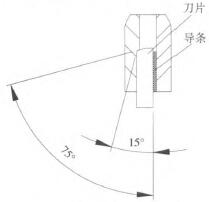
[size=10.9091px] 图7 MAPAL导管加工刀片
[size=10.9091px]
[size=10.9091px] 为证实上述分析是否正确,MAPAL做了5片钝化刀片做验证。这5片钝化处理刀片将精加工和修光刃两部分用刷子打磨进行刃口钝化处理‘61,如图8所示。
[size=10.9091px]
[size=10.9091px] 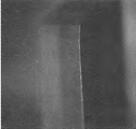
[size=10.9091px] 新刀片 钝化刀片
[size=10.9091px]
[size=10.9091px] 图8钝化精加工和修光刃刀片
[size=10.9091px]
[size=10.9091px] 测试方法是将这5片刀片上机床使用,并记录前面加工的13件工件中的第1件、第2件、第3件、第5件、第10件工件的各孔的直径数据值,同时观察是否有气门插不进现象发生。测试数据显示这5片在低于13件寿命之前全部出现“上小下大”,且出现“上小下大”频次和孔径与未进行钝化之前相差不大,虽然未出现气门插不进现象,但和目前在用的未钝化刀片数据对比没有改善,测试失败。数据见(表3)。
[size=10.9091px] 表3未钝化刀片和钝化精加工刀片测试数据
[size=10.9091px]
[size=10.9091px]
[size=10.9091px] 虽然测试效果不理想,但从测试数据可以看出,钝化精加工刀片所加工孔上下截面数据最大差值比未钝化刀片加工数据有所减小。只钝化精加工刀片所增加的径向力太小,不能使PCD导条可靠地贴紧已加工表面,仍需进一步加大径向力。
[size=10.9091px]
[size=10.9091px] 3.3钝化750粗Jjn-r刀片
[size=10.9091px]
[size=10.9091px] 对导管刀片加工过程各部分进行受力分析p J,由图9可知:
[size=10.9091px]
[size=10.9091px] 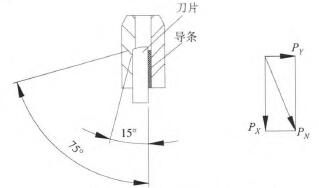
[size=10.9091px] 图9导管刀片加工过程各部分受力分析
[size=10.9091px]
[size=10.9091px] ①对精加工15。刃口部分进行分析
[size=10.9091px]
[size=10.9091px] PYl=sinl50PN=0.2588 PN
[size=10.9091px]
[size=10.9091px] 以1=eosl50PN=0.9659 PN
[size=10.9091px]
[size=10.9091px] ②对粗加工750刃口部分进行分析
[size=10.9091px]
[size=10.9091px] PY2=sin750PN=0.9659 PN
[size=10.9091px]
[size=10.9091px] PX2=cos750pN=0.2588 PN
[size=10.9091px]
[size=10.9091px] ③修光刃部分为0。,理论上受力为0,不与考虑。式中:Pl,一径向力;PX一轴向力;PⅣ一切削合力。
[size=10.9091px]
[size=10.9091px] 可见,对于径向力Py的影响,粗加工75。刃口部分要比精加工150部分大得多。
[size=10.9091px]
[size=10.9091px] 从实际加工情况分析,导管在加工时前面引导刀只是加工进导管7mm,后面一段毛坯余量还是较大,而导管刀片精加工加工余量很少,余量绝大部分都是750粗加工部分去除,可见75。粗加工部分刃口对加工之后孔的直线度起主导作用。
[size=10.9091px]
[size=10.9091px] 只要将750粗加工部分刃口钝化就能产生足够的径向力使得导条始终贴合已加工表面,从而保证加工孔的直线度要求坤J。同时精加工刃口未进行钝化处理,刃口锋利,有利于切削,对刀片的寿命也不会产生影响。为验证该分析,MAPAL重新做了5片只钝化750的刀片进行测试,这5片刀片都是用毛刷在转盘上对75。粗加工刃口进行2个小时的钝化处理,如图10所示。
[size=10.9091px]
[size=10.9091px]
[size=10.9091px] 新刀片 75。粗加工刃口钝化刀片
[size=10.9091px]
[size=10.9091px] 图10新刀片与75。粗加工刃口钝化刀片
[size=10.9091px]
[size=10.9091px] 用同样的测试方法,结果显示,5片测试刀片中均没有出现“上小下大”现象,效果对比先前有明显改善,与先前分析结果完全符合,5片测试刀片试切数据,见表4。
[size=10.9091px] 表4钝化75。粗Jju-r刃口ijn-r数据
[size=10.9091px] 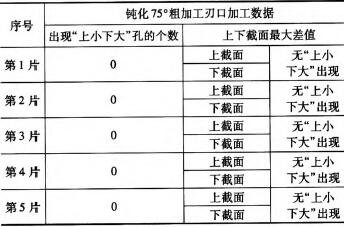
[size=10.9091px] 成功试切之后,又进行了50片的小批量测试,跟踪钝化750粗加工刃口刀片加工情况,刀片全部能达到1200件寿命,刃口磨损程度正常,基本没有出现“上小下大”等气门弯曲情况发生,加工效果与先前对比有了明显改善。
[size=10.9091px]
[size=10.9091px] 自2010年8月开始大批量使用750钝化导管刀片以来,装配再无反馈气门插不进情况发生,员工的换刀次数也大幅降低。因气门插不进造成缸盖报废的零件数量相比明显减小(见表5),至今售后也再无类似的投诉反馈。
[size=10.9091px]
[size=10.9091px] 表5气门插不进造成缸盖报废的零件数量
[size=10.9091px] 
[size=10.9091px] 4、结束语
[size=10.9091px]
[size=10.9091px] 通过对主流的MAPAL单刃导管孔刀具在气缸盖加工导管孔时出现的孔径直线度差‘91、气门插不进问题进行调研分析,指出单刃枪铰刀在加工过程中存在的缺陷‘101,并通过对其进行15。粗加工刃口钝化处理和750粗加工刃口来切削加工气缸盖加工导管孔并将效果进行对比。实践证明对单刃枪铰刀的750粗加工刃口钝化处理使刀具寿命增加、刃口磨损程度正常、基本没有出现“上小下大”等气门弯曲情况发生、装配时再无气门插不进情况发生,减少了生产线员工换刀次数和报废件的发生,降低了汽车运行中的安全隐患。
|