来源: 华东理工大学机械与动力工程学院 作者:吴松,何云,陈龙,李林宁
摘要: 通过对汽车发动机曲轴某一段主轴颈的加工工艺研究,以及对曲轴加工刀盘工作原理的分析,提出了刀盘结构的设计要求,并对刀盘单元切削模块进行了分类,实现了刀盘结构的模块化设计。针对车梳拉刀盘模块中的刀夹-刀盘组合进行尺寸链的优化设计,刀盘的尺寸公差值从原来的12μm放宽到25μm,制造的经济性和合理性得到了提高。根据曲轴加工工艺要求,完成了车-车梳( 拉) 实验刀盘驱动装置的设计和切削力校核。曲轴加工实验刀盘已成功应用于车-车梳( 拉) 切削实验。
关键词: 曲轴; 车-车梳( 拉) 刀盘; 单元切削模块; 装配尺寸链
0 引言
作为汽车发动机关键零件之一,曲轴的加工工艺和加工刀具的研究一直受到人们的广泛关注。车-车梳( 拉) 加工刀盘作为曲轴加工设备的核心部件,为曲轴的加工工艺研究提供了硬件保证。车-车梳( 拉) 刀盘在一次装夹中就可完成曲轴的法兰前端部位、主轴颈稳定带,主轴颈根切、曲臂的倒角以及主轴颈的齿轮环座的加工,加工效率高。在德国、瑞典、日本等国,车梳拉工艺以及车梳拉刀盘技术已经非常成熟,而国内车拉刀盘的研发仍处于起步阶段,相关的曲轴加工设备基本上依赖进口。所以,拥有一套完善的曲轴加工刀具系统是非常有必要的。
采用曲轴车-车梳( 拉) 刀盘加工曲轴具有以下特点[1]:①多刀切削,刀具寿命长。一个刀盘上装有多把刀片参与切削,加工时分配到每把刀片上的切削量少;如果其中某一个刀片失效,可以用刀盘上其他位置的同类刀片替换,不用卸载刀片重新安装,减少了刀具系统的重复装配次数。②粗精加工分类明确。刀盘上不同刀夹对应不同刀片,负责曲轴不同部位的粗、精加工。粗加工负责切除曲轴多余材料,精加工负责保证加工精度。③加工节拍高,生产效率高。做到一次装夹,能够完成主轴端面、轴颈、曲轴臂、平衡块、沉割槽等部位的半精加工,并可省去粗磨工序。根据以上特点,本文对刀盘的整体结构进行了模块化设计,并对刀盘的装配精度进行了优化,最后完成了刀盘驱动装置设计和刀盘粗加工时的切削力校核。曲轴加工实验刀盘的成功开发与应用,为曲轴加工设备的国产化奠定了基础。
1 、曲轴加工刀盘模块化设计原理
1. 1 曲轴主轴颈加工工艺分析及刀盘加工原理
曲轴主轴颈的加工需要经过多道工序,一般的主轴颈加工工艺流程如图1 所示,图中虚线部分为待加工表面,每道工序中所示加工刀具即为完成该道工序所使用的单元切削模块。在曲轴车梳拉加工过程中,所有工序加工刀片同时安装于刀盘体上,通过编程的方式将曲轴车梳拉加工所有工序编程至同一个程序中。程序启动后,刀盘根据程序设定旋转至指定刀夹工作位置,进行切削加工,当此道工序完成后,刀盘又旋转至下一刀夹位置进行加工,直到加工程序结束为止。
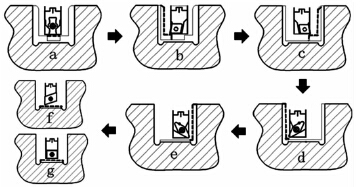
图1 曲轴主轴颈加工工艺流程图
车-车梳拉加工工艺实际上由车削加工和拉削加工组合而成。车-车梳拉加工工艺前几步采用车削加工,最后一步采用车梳或车拉加工。车削原理基本相同,机床主轴带动曲轴工件高速旋转,刀盘待加工刀片刀尖旋转到曲轴回转中心,然后向曲轴作径向或轴向进给运动,切削量由进给量确定。车梳与车拉工艺的主要区别在于加工过程中刀盘的运动方式不同。车拉加工过程中,曲轴工件围绕机床主轴高速旋转的同时,车拉刀盘旋转到车拉刀夹后径向向曲轴作进给运动,切入工件后刀盘按一定转速随动旋转切削,从而实现刀盘的车拉加工,刀盘旋转的角度为切削刃长度对应刀盘角度; 车梳加工过程中,刀盘旋转至梳刀位置后静止,径向进给一个齿升量进行梳削,然后轴向移动一个齿间距进行车削,这样往复交替进行复合加工。
1. 2 曲轴加工刀盘设计要求
车-车梳( 拉) 刀盘是曲轴主轴颈加工工艺中最重要的设备之一。国外常见的车-车拉刀盘结构见图2。
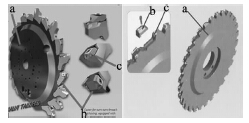
图2 国外车-车拉刀具
对国外几家知名企业的曲轴加工刀具结构进行分析可知,曲轴加工刀盘可分解为刀盘体和单元切削模块两部分组成。刀盘体是单元切削模块的载体,负责与机床连接并为单元切削模块提供空间安装位置。单元切削模块可分解为刀夹和刀片。单元切削模块根据选择刀片的不同,对应不同的刀夹,从而实现不同的切削功能。刀夹负责为刀片提供夹持力和安装位置角度。为了实现模块化构型设计,方便单元切削模块的更换,刀夹与刀盘的装配要求采用统一的定位和固定方式。不同的刀夹可以在刀盘的不同位置自由安装。通过改变刀盘体上面单元切削模块的种类和加工顺序,可以满足不同曲轴的加工要求。
1. 3 曲轴加工刀盘的模块化分解
通过对曲轴主轴颈加工工艺和刀盘设计结构的分析,完成曲轴主轴颈的粗加工与半精加工需要多种单元切削模块参与切削,一个完整的车-车梳( 拉) 刀盘集成了曲轴主轴颈半精加工所需的全部单元切削模块。根据单元切削模块的加工精度将其分为两大模块: 粗加工模块和半精加工模块。同时粗加工模块根据其加工曲轴部位不同分为开槽刀夹、粗车轴颈端面刀夹; 精加工模块根据其加工部位不同分为半精加工沉割槽刀夹、半精加工主轴颈刀夹( 如图3) 。
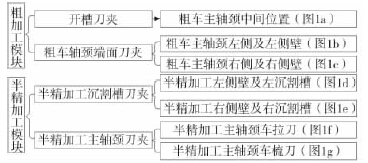
图3 单元切削模块
曲轴加工刀盘的模块化分解为刀盘的构型制造提供了理论基础,加快了刀盘的制造速度,缩短了曲轴工艺的研发周期。
2 、曲轴加工刀盘模块化构型设计
车-车梳( 拉) 刀盘的模块化构型设计包括刀盘体设计和单元切削模块的设计[2]。
2. 1 刀盘体结构设计
由于实验机床设备的限制,刀盘体直径不能够设计的很大,因此限制了刀盘体上安装刀夹的数量,但仍能够实现曲轴主轴颈的整套加工工艺需求。另外,刀盘体与刀盘驱动装置通过定位销定位,采用螺钉方式连接,连接可靠,易拆卸。刀盘体经有限元分析[3],符合曲轴加工刚度要求。刀盘结构示意图如图4。
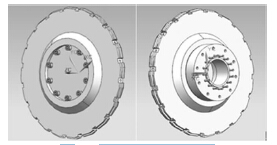
图4 刀盘体结构示意图
实验刀盘体主要参数如表1 所示:
表1 刀盘体尺寸及材料参数表

2. 2 单元切削模块的设计
单元切削模块是车-车梳( 拉) 刀盘模块化设计的关键,单元切削模块设计的合理性直接决定了刀盘的加工柔性。
单元切削模块主要由刀夹和刀片组成。由于采用的是自主设计的刀盘,因此需要设计一套与刀盘体相配合的刀夹。
刀夹是连接刀盘、传递扭矩的关键部位,刀夹的定位精度影响了曲轴的加工精度。由于刀夹需要根据不同工艺需求经常进行更换,因此单元切削模块的刀夹与刀盘的连接方式必须一致,而且要求定位精确,具有良好的可拆卸能力。设计刀夹采用键定位传力,上螺栓固定夹紧( 偏心夹紧方式) 。
刀片是易损件,也需要经常更换,采用螺钉连接设计,方便拆卸。刀片都选用常见的车削刀片( 少部分刀片为特制刀片) 。刀夹与刀盘体的连接部位根据刀盘体结构设计,刀片在刀夹上的固定结构根据刀片形状设计。图5 为粗车轴颈端面刀夹的安装方式示意图,图6 为粗车轴颈端面刀夹对应刀片的安装方式示意图。
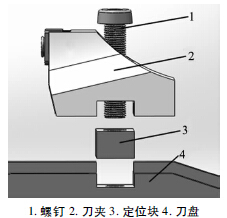
图5 刀夹安装方式
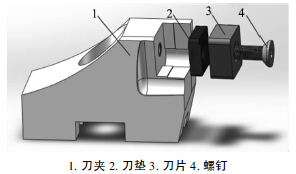
图6 刀片安装方式
3 、刀盘模块精度优化
由于曲轴加工精度要求较高,因此刀夹与刀盘的制造精度有要格的要求。为了提高刀盘-刀夹制造的经济性和合理性,现针对车梳拉刀盘模块的装配尺寸链进行建模,对刀夹-刀盘的制造公差进行优化。
由于刀夹定位块与刀盘体紧密配合,不影响刀夹尺寸链的计算,因此为了简化模型、方便计算,将定位块和刀盘视为一体。刀片-刀夹-刀盘模块的立体图如下左图所示,刀片-刀夹-刀盘模块的装配平面示意图如图7 所示。
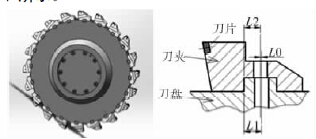
图7 刀片-刀夹-刀盘装配示意图
如图7 右图,刀夹装配在刀盘上,刀夹上的螺钉孔的中心线与刀盘螺纹孔中心线有一个偏移量( 偏心夹紧方式) ,偏移量大小在由装配后刀夹和刀盘的尺寸L2 和L1 决定,所以偏移量L0 可以作为封闭环,其中基本尺寸L2 = 7mm,L1 = 7. 1mm,通过分析可知,L1 为增环,L2 为减环,L0 为封闭环。各环之间关系为: L0 =L1 - L2 = 0. 1mm。
由于封闭环的公差是最大,所以对封闭环设定较低的精度等级,通过查询公差等级表及实际制造经验,将封闭环公差设定为50μm( 介于IT10 ~ IT11 级之间) 。然后选用相等精度法[4]计算两组成环公差因子。
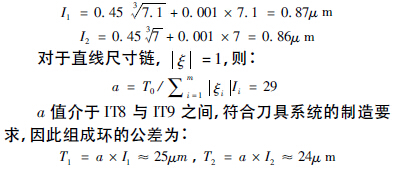
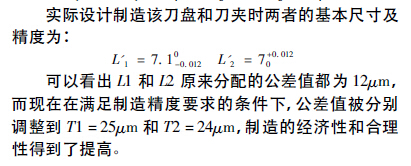
4 、刀盘切削力校核及切削实验应用
4. 1 刀盘驱动机构分析及设计
改造原有的数控机床( 机床型号: CH7520,如图8所示) 刀塔部位。利用原有的数控机床刀塔与机床的接口与控制部位,在其基础上重新设计一个自带电机的动力转台( 由伺服电机驱动) 。动力转台与车-车梳拉刀盘结构连接,从而实现刀盘的普通车削、车梳( 拉) 加工功能。改造后刀盘实物图如图9。
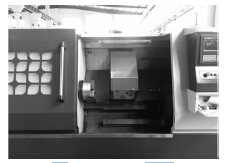
图8 CH7520 机床
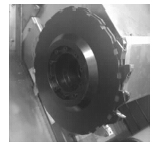
图9 刀盘实物图
由刀盘的切削原理可知,刀盘驱动装置不仅仅需要一个可以使刀盘旋转的旋转轴,还需要一个可以使刀盘沿着径向运动的轴。在此选择一级蜗杆传动作为车拉刀盘驱动装置的主形式。一级蜗杆传动的传动比大,蜗杆与蜗轮啮合处润滑较好,传动平稳,没用噪音,结构紧凑,环境适应性好,且单头蜗杆传动具有重要的自锁性。在蜗轮蜗杆传动形式中,选择平面二次包络环面蜗杆传动。这种蜗杆传动承载功率大,传动稳定,噪音小、平衡温度低,具有普通蜗杆减速器所不具备的很多优点。一级蜗轮蜗杆示意图见图10。
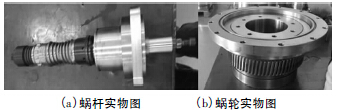
图10 转台蜗轮蜗杆示意图
转台设计装配图见图11。
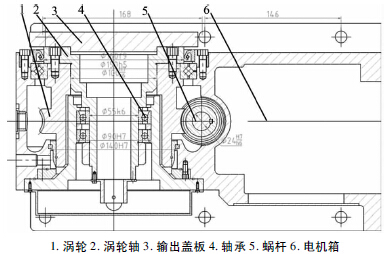
图11 转台装配图
电机可安装在转台右侧空间位置,电机通过转台带动刀盘的旋转。刀盘与转台通过螺栓连接。
4. 2 刀盘切削力校核
由于刀具在切削过程中,刀盘所受载荷可通过刀夹刀片受力来分析计算,前刀面和后刀面都受到切削力的作用,切削力包含切削力Fz、背向力Fy、进给力Fx,常用车削切削力指数公式形式如下[5]:
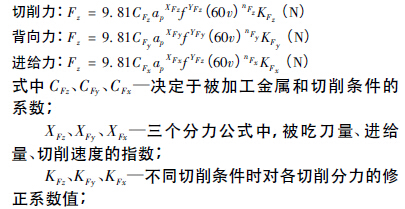
v—单位为m/min。
假定实验加工曲轴材料为调质钢,刀具为硬质合金,加工形式为切削外圆,切削参数选取粗加工切削参数,即v = 150m/min,ap = 1mm,f = 0. 1mm/r,公式参数可通过工具书查阅得知[6],因此代入公式计算如下:
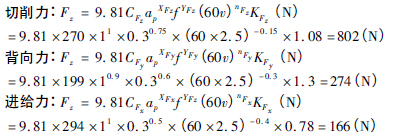
以上算出值为刀盘在粗加工过程中产生的切削力。刀盘直径为380mm,可知:刀盘粗加工时,刀盘主轴受到扭矩:M = FZ·D/2 = 152. 38N·m由4. 1 中设计的刀盘驱动装置达到的传动扭矩为1140N·m,大于刀盘粗加工时的扭矩,刀盘系统设计满足曲轴加工需求。
4. 3 刀盘的切削实验应用
刀盘的模块化设计为曲轴加工工艺设计和实验研究提供了一个有效的试验平台。通过刀盘试验平台的建立,进行了以下几个方面的实验研究:
( 1) 利用刀盘对曲轴常用材料QT700-2 进行车削模拟试验,研究了单元切削刀具的主要失效形式和磨损机理,建立单元切削刀具寿命模型,并对具有不同刀尖圆角半径的单元切削刀具进行了对比试验[7]。
( 2) 利用刀盘进行车拉切削模拟实验,对轴向切削力Fp 与工件加工后圆度? 进行测量,推算出材料去除率MRR、稳定刃宽Bw 的估算公式。并研究总切深和进给量对于这四个参数的影响[8]。
( 3) 利用刀盘模拟曲轴车梳切削实验,研究不同齿数的梳刀对刀片切削性能的影响[9]。
( 4) 利用刀盘模拟曲轴车-车拉工艺和车-车梳工艺的对比实验,分析两种不同加工工艺对曲轴主轴颈加工精度、粗糙度和加工效率的影响[10]。
5 、总结
( 1) 曲轴实验刀盘由刀盘体和单元切削模块两部分组成。在刀盘体上选择不同的单元切削模块与安装方式,可以满足不同曲轴的工艺需求。刀盘的模块化设计为曲轴加工工艺设计和实验研究提供了一个有效的试验平台。
( 2) 合理的设计刀盘-刀夹的制造精度,可以提高制造刀盘与刀夹的经济性和合理性。本设计中刀盘和刀夹的制造公差值被分别调整到T1 = 25μm 和T2 =24μm。
( 3) 针对配套刀盘切削载荷问题,以刀盘切削参数为基础,根据切削力指数公式对刀盘切削载荷进行了计算。结果表明: 切削过程产生的切削力矩在转台的传动扭矩之内,能够满足曲轴加工需求,并可进行曲轴切削模拟实验。
|