2015-9-11 来源:第二汽车制造厂柴油发动机厂 作者:柳立康
近十多年来, 第二汽车制造厂( 以下简称二汽) 从国外引进的技术项目共三十多项, 其中以引进美国康明斯( C o m l n ni s ) 公司的B 系列柴油机和联邦德国许勒一惠勒(H 叭1e r 一H il el ) 公司的组合机床设计制造技术为两个最大的项目。围绕着柴油机的开发, 二汽不仅引进了产品和关键工艺, 也引进了不少关键设备, 特别是从许勒一惠勒公司引进的组合机床设计制造技术, 在二汽的柴油机厂得到了广泛的应用。
本文只想通过介绍 1 5 3 柴油机缸体加工工艺和所用设备的一些特点, 使读者对二汽近年来的技术发展状况有一些了解。
1、产品简介
E Q 土5 3柴油机是二汽近几年从美国康明斯公司引进的新产品。康明斯公司有80 多年的历史。它生产的柴油机不仅在美国国内占汽车柴油机产量的以上05 , 而且在世界柴油机市场上一也占有很重要的地位, 它在14 3个国家设有服务网点, 其中有6 个国家有它的子公司生产其产口口目。我厂引进的是康明斯公司刃系列的4缸、6 缸柴油机。刀系列柴油机是19 7 8年8月开始研制的,19 84 年7 月投入市场, 与世界上同类产品相比, 各项性能指标可以说都是比较先进的, 具有80 年代中期世界先进水平。它有很多特点、现把与缸体加工有关的一些特点作一简单的介绍石( 1 ) B 系列柴油机结构简单, 品种数量少。其水泵壳、机油泵壳、机油冷却壳、机油滤清器底座、燃料滤清器底座以及冷却器小循环管路都和气缸体组合铸造在一起;( 2 ) B 系列柴油机外形尺寸紧凑, 重量指标先进。例如6 B T A 机型1 86 马力/ 2 8 0 0转, 重量仅为4 l l k g。
缸体采用薄壁结构, 且取消了缸套、凸轮轴衬套( 但均留有余地在大修时可镶套) 多( 3 ) B 系列柴油机主要零件的加工精度, 要求并不很高, 比较容易实现。现将刀
系列柴油机缸体的主要加工精度和二汽老产2 缸体生产线的概况l异: E Q 6 1 0 0 的缸体作一比较, 如表1 所列。
表1
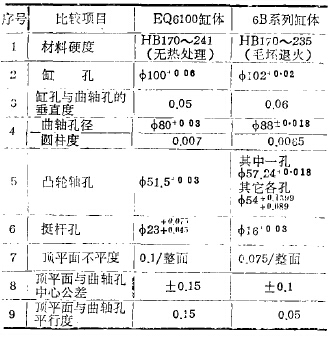
2、缸体生产线的概况
1 ) 生产规模生产规模决定了生产组织和加工手段,我厂E Q 1 5 3 柴油机年产纲领6 万台, 其中6缸5 万台4 缸1 万台, 二班制生产, 生产纲领不算太大。缸体加工车间共有自动线13条, 组合机床单机8 台, 专用设备1 台, 非标设备7 台( 不包括生件、铁屑的输送以及粉尘的排除设备)。
( 2 ) 生产线的特点工艺设计中借鉴了康明斯公司推荐的工艺, 且结合国内的实际情况安排的, 生产线有如下一些特点:
① 依据6 万台的生产纲领, 为了减少设备数量, 在节拍允许的条件下, 大量采用了双工位机床;
② 为了便于组织生产, 也为了减少设备台数, 迄E、6 B 二种缸体的加工要求在生产线上能够同时通过( 其中4 B 专用设备3 台)
③ 由自动线、单机组成的生产线之间实行柔性连接, 从而具有一定的中间储备能力, 保证了全线能连续、稳定地运行,
④ 自动线的工作范围不限于单纯的切削加工, 在自动线内已纳入了检测、油道孔试验等工序;
⑤ 生产线中大量地采用了枪钻、枪铰工艺。为了减少工位数、设备台数以及便于冷却润滑液回收, 改善生产环境, 枪钻、枪铰与攻丝组台在一起, 组成4 条湿式( 即采用冷却液的) 自动线, 除这4 条线外, 其它组合机床与自动线没有采用冷却液, 即所谓的干式加工;
⑥ 铁屑处理采用地沟刮板式的。对于干式加工, 切削加工中产生的粉尘, 采用上抽风的方式排除, 而康明斯公司采用的是下抽风式的。下抽风式的吸尘效果较好, 山于下抽风铁屑与粉尘是在同二通道中通过, 铁屑在输送过程中产生的粉尘能随时被吸走,而上抽风的抽风范围有狠大的局限性, 且排出的粉尘直接被排放到大气中, 污染了周围的环境。上抽风的管道在车间林立, 对工人的操作和维修都带来许多不便。虽然下抽风有那么多优点, 但目前国内采用它条件还不具备, 因为现有的组合机床通用部件, 不能满足下抽风对设备提出的要求;
⑦ 在整个缸体生产线中, 加工设备以卧式为主, 这对一切屑的排除创造了方便条件;
⑧ 缸体生产线中, 采用了不少新工艺、新技术和新设备, 其中包括引进的两条精加工自动线和一台缸孔小平顶布磨机。另外, 三座标测量机和数控设备在生产线中也已被采用。
( 3 ) 缸体加工的工艺流程
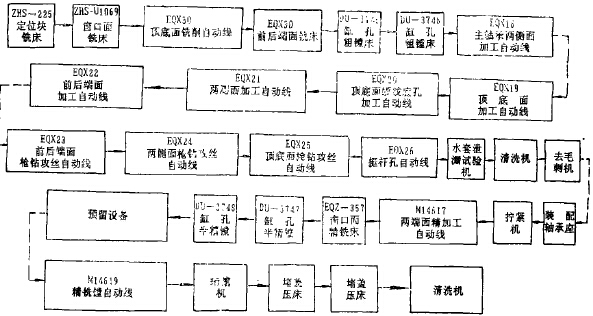
图1
工艺流程直接关系到加工质量、工作的可靠性及经济效果。现将6 B 缸体的工艺流程作一简介, 其设备布置如图l 所示。Z H S 一咒下: 是一台数控设备, 铁削定位用的凸台面。Z H S 一U 10 9 : 单机, 名t 削侧面的窗口面、文架平面, 这些加工面, 在后面的工序`{,, 可做为工艺基准面和工艺导向面。E Q 丫1 7: 由5 台主机组成的自动线, 精铣顶底面、主轴承结合面、主轴承半圆孔、半精铣底面、钻扩饺工艺定位销孔。E Q X 3。: 是由1 台主机与输送机构组成的铣床, 粗铣前后端面。D U 一3 4 7 53 4 7 6用于粗铿缸孔的2 台单` 机。E Q 人18: 由6 台主机组成的自动线, 粗铣主轴承二侧面瓦片槽、凸轮轴键杆支架空隙、回油孔。精铣底面、主轴承结合面和主轴承二侧面。E Q X 19 : 由5 台主机组成的自动线, 钻饺活塞喷油孔及部分顶底面的螺纹底孔和推杆孔的加工。E Q X Z O: 由5 台主机组成的自动线, 完成顶底面余下的螺纹底孔及扩铰定位环孔。
E Q 入2 卜由5 台主机组成的自动线, 铣削进水管冷却器和燃油泵的安装平面和所有两侧面螺纹底孔的加工。E Q`2 2.由5 台主机组成的自动线, 粗加工凸轮轴孔、油泵孔、水泵孔。粗精加工出砂孔和加工两端面全部螺纹底孔。
E Q X 2 3: 由3 台主机组成的自动线, 枪钻主油道孔和两端面所有螺纹孔的攻丝。E Q 戈2’f : 由4 台主机组成的自动线, 枪钻水冷却器进油孔, 钻油孔, 钻铰油标尺孔和两侧面所有螺纹孔的攻丝。E Q X 2 5 : 由5 台主机组成的自动线,枪钻顶底面的深油孔和顶底面所有螺纹孔的攻丝。
Q X 6 2 由台主机组成的自动线4 , 钻、枪铰、铰顶杆孔。E Q X 2 3、E Q X 2 1、E Q X 2 5、E Q X 2 3四条自动线都是采用冷却液进行加工的, 即所谓湿式自动线。水套泄漏试验机, 多工位专用清洗机,去毛刺机, 轴承座装配机, 螺栓拧紧机都安装在这四条自动线的后面。M 14 6 17 :由5 台主机组成的自动线, 完成两端面的精铣以及曲轴孔、凸轮轴孔、水泵孔、油泵孔、惰轮孔、定位销孔、主油道孔的半精加工和精加工。此线由英国克劳斯公司提供。E Q Z 3 5 7: 是一台单机, 精铣窗口面、支架平面和工艺导向面。D U 一3 7 4 73 7 4 8: 是用一于半精锉缸孔的两台单机。
M 14 6 19 : 缸孔和顶面的精加工自动线。
此线也是由英国克劳斯公同提供的。
3 V 5 8一50 2 A : 缸孔小平顶布磨机, 由联邦德国N A G E L 公司提供。对主轴承孔的超精加工工序在工艺上已有安排, 但因设备制造厂家暂时没有落实,为此暂不留加工余量。
3 、缸体加工工艺和刀具的
一些特点缸体是形状复杂、精度要求高、刚性差工艺性差的壳体型零件, 其加工工艺复杂,下面按加工分类分别对其在工艺安排上和所用刀具等方面的一些特点作一介绍。
( 1 ) 平面加工中的特点
缸体中有不少需要加工的大平面, 由于有配合关系及工艺上的需要, 精度和光洁度往往要求比较高。
而且大面积的平面加工还直接影响着整个缸体的加工节拍时间。二汽对缸体大平面加工的传统方法是:
粗加工采用拉削, 它生产率高, 加工质量也很稳定。
但是随着新型优质刀具材料的开发, 新型铣刀结构— 密齿端铣刀的应用,以及铣削机床结构性能的改善, 使铣削加工越来越被广泛地采用。与拉削比较, 它适应范围广, 机床布局灵活, 结构简单, 维修方便。
为此缸体平面所有粗精加工, 我们都采用了铣削。
铣削所用的刀具, 主要采用不重磨硬质合金刀片, 其刀具寿命高, 刀片不需焊接, 当刃口磨损后, 不必从机床上取下整个铣刀重磨, 只需把刀片转换角度或调换新的刀片。在铣刀中还装有修光刀片, 这是一种用宽1.4 m m平行修光刀棱代替刀尖圆角刃的刀片。当铣刀的每转走刀量小于平行修光刃宽度时, 修光刃刀痕所形成的平面会互相连续重叠, 此时只需一片修光刃即可, 否则需增加修光刃片数。修光刃刀片比其它刀片高出0.02 m m。
我们所用的铣刀, 大部分是国产的, 个别精铣刀是从瑞典山特维克购进的。山特维克的端铣刀, 固定座直接装在刀盘上, 周向、径向和轴向三个面都靠紧, 是不可调节的,因此刚性很好。铣刀的端面跳动对加工质量影响甚大, 因而对刀盘和刀片的精度要求都非常高。在E Q X 30 自动线中, 粗铣缸体两端面的机床上就采用了这种结构形式的、国内制造的刀盘, 但精度保证不了加工要求,其端面跳动往往在0.l m m 以上。山特维克铣刀的端面跳动一般可达到扣.0 肠m m。国内制造的这种结构形式的铣刀盘, 虽可精调到0.瞬m m 以下, 但精调所获得的精度是通过转动刀片取得的, 因此精度极易走失。在E Q X 30 自动线调试中, 当加工10 个工件后,就因为刀片移动, 造成加工表面光洁度明显下降。国内的铣刀盘结构一般采用通槽, 沿轴向是可以调整的, 通过调整, 来保证铣刀端面跳动的高要求。但这种结构刚性差, 在试生产中, 当切削余量较大时, 发现铣刀的精度经常会走失, 有时加工后铣刀的端面跳动超过了0.1mm刀片夹紧形式, 山特维克的铣刀采用的是弹簧拉紧楔块的结构。这种夹紧方式更换刀片方便, 拨动弹簧即可把刀片取下。
国内制造的铣刀盘也有采用这种结构的, 但质量还不过关, 常采用的是螺钉压紧楔块。按照康明斯公司的工艺安排, 铣削加工机床除顶面的精加工以外皆采用卧式机床,这样不仅便于排屑, 设备刚性也好。铣削时铣头安装在带侧置底座的机械滑台上。工件一般都不动, 夹具固定在中间底座上, 其精度、刚度容易得到保证, 而且对与夹具油缸连接的油管在排列上也带来了许多方便。
但是在两端面粗铣时却采用了不同的方式, 夹具安装在带中间底座的机械滑台上, 随着滑台移动。铣头则固定在两侧的底座上。这样要求输送机构直接把工件输送到夹具上, 待工件定位、夹紧后, 机械滑台再实现进给运动, 减少了工件的两次转位。为了能适应4 缸和6 缸两种缸体的加工, 分别采用了两种不同的铣头, 即滑套式铣头和滑座式铣头。滑座式铣头可以移动很大的距离, 因而可满足4 缸和6 缸两端面之间不同距离的加工要求。
为了减少机床台数, 在加工缸体侧面的冷却器安装面、机油过滤器安装面、进水管安装面、燃油泵安装面时, 粗精加工安排在同一台设备上完成, 分别由两把铣刀进行粗加工和精加工。铣削冷却器安装面和进水管安装面时,由于工件形状的限制, 铣刀只能上下移动进铣头行铣削, 由铣头沿导轨作上下运动来实现,如图2 所示, 而机床结构与卧锉相似
。
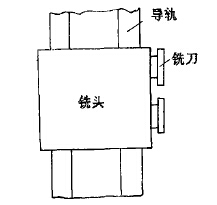
图2
为了保证主轴承结合面到底面的距离, .按照康明斯公司的工艺安排, 底面和主轴承结合面组合在一起加工, 而且粗加工后即在底面上加工定位销孔。由于粗加工时切削力
很大, 而工件的刚性很差且又需要有很大的夹紧力(见图3 ) , 加工时在中间位置又是无法加以支承的。
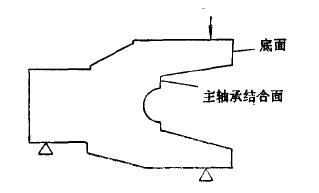
图3
因此工件必然会产生很大的弹性变形, 为此我们在粗加工后, 增加了一台底面的半精铣, 然后再进行定位销孔的加工。康明斯公司在加工底面和主轴承结合面时, 采用了复合刀具, 两把铣刀套装在同一轴上。由于两把铣刀的直径相差很大, 分别为小15 0 m nr 和小4 o om m , 因此, 切削时的切削速度会相差很大。
设计制造这样的复合刀具及相应的主轴结构, 在主轴箱设计中有很大的难度。而现在我们采用了两把铣刀, 左右排列相距i 3 3Om m , 小铣刀先切入工件,对主轴承结合面进行切削,然后大铣刀紧跟而上, 对底面进行切削。
这样进行切削就会出现三种情况: ① 小铣刀单独工作; ②小铣刀和大铣刀同时工作; ③大铣刀单独工作。三种状况加工的质量是不会完全相同的, 当初我们最担心的是第二种情况, 大小铣刀同时工作是否会产生干扰呢? 结果与判断的正好相反, 第二种情况加工的质量最好。我们分析其原因, 大概是由于小铣刀切削时产生的切削力起到了紧固工件的作用, 因而工件的振动反而小了, 从而改善了在大铣刀切削底面时的工作条件。缸体生产线上的第一道工序是铣工艺凸台、工艺导向面及四个凸台平面, 因高度不同原设想采用5 把铣刀同时切削。采用这样的方案, 设计和制造都有一定的难度, 也不易保证加工面之间的高度公差。最后决定改变原设计方案, 采用数控设备由1 把刀代替5 把刀的工作。在生产线中采用数控设备,对我厂来说一也是一种新的尝试。由于铣削加工的冲击力大, 振动大, 温度变化也大, 因此不仅对机床的刚性, 特别是对主轴系统的静态刚度和动态刚度有较高的要求外, 对主轴精度特别是端面跳动也有严格的要求。此外工件的刚性、振动特性,工件的可夹紧性, 铣刀本身的刚性和精度,以及切削速度, 刀具材料等对铁削精度都会产生很大影响。
( 2 ) 一般孔加工中的特点缸体所要加工的孔很多, 工作量相当大,除了采用传统的加工方法外, 我们在缸体生产线中大量地采用了枪钻加工工艺。枪钻加工主要用于对缸体上的主油道孔及与主油道孔相通的各油孔和水冷却器进油孔。这些孔都属细长孔, 对细长孔加工的传统方法是采用分级进给, 这样所加工出收孔一般都带有台阶。这些孔中的台阶在使用时容易滞留杂质, 而发动机油道孔的清洁度要求是非常高的, 所以对于油孔我们都采用了枪钻加工。主油道孔长g 8 8 m m , 为了保证生产线的节拍时间, 我们采用从两端同时加工的办法。为.了避免在对接处留下台阶, 对枪钻孔的位置精度和孔的直线度都有一定的妥求。用枪钻加工与主油道相通的孔时, 导向套很难贴紧工件并实现密封。当带着切码的切削液沿刀杆排屑沟返回时, 很容易从贴合面处喷出。
部分流经导向套的冷却液, 压力减小了, 流量减少了, 容易造成切屑滞留在导向套内, 加剧了刀具与导向套的磨损。目前除了采用可伸缩的导向套( 即每个导向套都有一个小油缸推动) 靠近二L 件以外, 还没有想出更好的办法, 枪钻加工对我们厂来讲还是一种新工艺, 需要我们不断的摸索, 总结经验, 以便进一步扩大枪钻的使用范围。对于缸体上的大多数孔来说, 仍旧采用的是麻花钻加工, 虽然如此, 但由于现在使用的机床精度提高了, 所加工孔的质量也有了一定的提高, 这具体体现在钻头直径的选择上, 选择的钻头直径越接近所加工孔的上偏差, 钻头修磨的次数就会越多, 经济性越好。
但同时在加工中出现超差的可能性也越大, 因此要求加工的水平越高。我厂选用钻头的直径虽然和国际先进水平比较还有一定差距, 但比过去显然有很大提高。例如加工直径为小6.6 5一小6.87 m 。的孔, 美国康明斯公司选择钻头直径为小.6 s m m , 我厂以前选为小6 7二m , 现采用小6.7 石m m。对于深孔加工所用的分级进给机构, 采用了从联邦德国引进的技术。
根据孔的精度要求不同, 采用了不同的加工工艺, 对精度要求较高的螺纹底孔, 钻孔后还需要铰孔。对有一定装配关系的水套孔则采用了扩和铰。对精度和位置精度都要求比较高的工艺定位孔, 采用了钻、扩、铰, 由于这些加工方法和传统沉加工方法区别不大, 在此就不再一一叙述。对于螺纹孔的加工, 我厂过去一直采用传统的压簧攻丝靠模机构。
由于靠模螺母与丝锥的螺距虽然名义尺寸相同, 但之间不可能没有误差, 因此在攻丝卡头和支承套筒内均装有压力弹簧。当靠模杆回转时, 通过靠模螺母产生进给运动。压力弹簧可使心杆、靠模杆能够有微量的轴向串动以补偿螺距误差。
采用这种机构在开始切削时, 丝锥并不是强制攻进的, 而常常在孔口处打滑。当用多轴箱攻丝时, 各丝锥与底孔的偏移量各不相同, 丝锥钝化程度不同, 补偿弹簧的质量也不相同, 这样造成切入的时间不能完全相同, 因而常常可造成2 至3 扣螺距的深度误差。在生产中也有采用由拉簧补偿的攻丝机构。此机构当丝锥在开始切入时是强制攻进的, 因而螺纹深度容易得到保证, 但螺纹精度却要低于由压簧补偿的攻丝机构。由拉补偿的攻丝机构, 其靠模螺纹比丝锥公称螺距减小1 一2%。
丝锥切入工件以后依靠自旋作用实现自身的进给运动, 丝锥的进给速度大于靠模杆的进给速度, 因此拉力弹簧被拉伸以补偿与螺距之差, 被拉伸的弹簧所产生的轴向力容易造成啮齿, 从而破坏了加工精度。
由于压簧、拉簧攻丝机构各有自己的优缺点, 因而产生了具备拉簧与压簧两个补偿环节的攻丝机构。它既能保证攻丝的深度, 又由于压簧的作用减小了拉簧所产生的轴向力, 从而也能保证攻丝的精度。我厂采用的攻丝卡头2 2 B F 石一8 8 是由许勒一惠勒公司的标准转化的, 其机构就是引用了上述的原理。2 2 B F 5 一8 8攻丝卡头采用滑块式方销传递扭矩, 因而有一定的浮动量, 从而可克服由于丝锥和底孔不同心所产生的偏移力, 起到了保护丝锥的作用。2 2 B F g 一8 是与攻丝卡头相配的快换卡头。它是依靠碟形弹簧压紧后产生的磨擦力传递扭矩的, 起到了过载保护作用。其压紧力的大小是可以调节的。山于许勒一惠勒公司的攻丝卡头和快换卡头是最近才转化的, 目前只有适用于加工皿拓一」n Z 螺纹孔的规格。其它尺寸的螺纹孔加工还仍然采用传统的攻丝卡头。由于钻头和丝锥的刚性较差, 常常容易折断, 为了及时发现加工中钻头的折断, 排除攻丝加工中的隐患, 攻丝前设置了孔深检测装置, 采用探针进行检查。并且有压缩空气通过探针中的通孔呆清除孔中的切屑。
( 3 ) 高精度孔加工的特点
缸孔加工的质量对发动机的基本性能有很大影响, 其精度要求又很高, 因而在缸体加工中, 缸孔的加工占了重要位置。缸孔的粗加工一般都采用锐削, 粗锐缸孔去掉铸件硬皮后, 工件的内应力会重新分布, 从而容易使工件产生变形, 为了避免变形影响加工精度, 同时又可及早发现铸件内部的缺陷, 粗锤缸孔工序要尽可能的安排在其它工序的前面。
粗铿缸孔时的切削力很大, 因此要求设备具有足够的刚性, 为此我厂采用了二台立式三轴膛床, 代替了一台六轴锉床的工作,这样可加大相邻主轴之间的间距, 从而可加大主轴的直径和轴承外径, 以提高主轴系统的刚性。滑座导轨采用了兰方向三导轨包容式结构, 导轨面也要尽可能加宽, 两侧导轨面各自的宽度已达30 0 m m , 而且两侧导轨面和进给动力头的主轴轴线距离非常小, 仅为3 3m m , 几乎在同一平面内, 因此切削时构成颠覆力矩的力臂非常小。
另外底座、立柱的刚性也非常好, 采用了封闭式的箱体结构。粗锤和半精撞缸孔的设备是由同一个厂家设计制造的, 为了减小设计制造的工作量, 同时也为了今后的维修方便, 粗锐和半精铿机床的结构是完全相同的。都采用了由液压滑台实现进给运动, 抗振性能好, 也便于实现倒角刀片的伸缩。
我厂生产的B 系列柴油机缸体, 其缸孔不镶套, 因此缸孔的上端不倒角, 而在其下端倒角, 为此, 在半精幢缸孔时, 在锤杆上设有二个刀片, 这二个刀片相隔一定距离, 前面的刀片对缸孔进行锐削, 当锐削快结`束时, 后面的倒角刀片在斜锲的作用下伸出进行倒角。-缸孔的精加工工序要求很高, 为了保证稳定的加工精度, 我厂从英国克劳斯公司引进了一条顶面和缸孔精加工自动线, 为了保证顶面与缸孔的垂直度, 减少毛刺, 精铣顶平面安排在精键工序的前面,`精铣和精锉都采用了高速切削, 为此所用的刀具都是采用立方氮化硼刀片。
为了保证加工质量, 在自动线上设置了测量工位, 可进行自动测量和半自动补偿,所谓半自动补偿, 即在自动测量装置中设有信号报警系统, 当刀具磨损超差时, 可自动发出信号, 提醒操作人员进行调刀, 由操作人员按动电钮, 每按动一次补偿量为1卜: m ,以补偿刀尖的磨损。这种半自动补偿装置,具有经济、可靠、简便的特点。精加工自动线中缸孔的第二次半精加工和精加工, 是在同一台机床上完成的, 先由半精铿键刀加工, 当半精膛键刀退出切削后, 精加工的撞刀从镬杆中伸出, 在主轴返回行程时进行切削, 这就是所谓的拉铿。拉锉时的搅杆处于受拉的应力状态, 刚性比较好。精铿的设备与粗幢一样, 也采用了立式三轴撞床。
不同的是精锉床6 个缸孔是在同一台机床上完成的, 当加工完3 个缸孔后通过移位再加工另外3 个缸孔。缸孔精加工的最后一道工序是瑜磨, 近几年来, 我国已引进了国外70 年代发展起来的小平顶琦磨技术。所谓小平顶琦磨就是把缸筒表面最顶尖琦成小平面, 以支承活塞和活塞环的运动, 其支承面积比普通布磨平均大2 5倍左右, 这样就大大提高了发动机的使用寿命。粗琳基础光洁度的深谷可存机油,有利于油膜的形成, 这样不仅缩短了新发动机的跑合时间, 也大大减少了发动机的机油耗量。
小平顶琦磨是采用复合式布磨头, 瑜磨头上装有粗琦、精布两套油石, 各自由单独的油缸控制, 首先粗琦形成平面的基础光洁度, 然后精布峰尖削成小平面。传统的布磨机由于工件在而磨时各处磨削的时间不同, 油石各处磨损也不相同,工件在经过琦磨后容易出现几何精度的超差。而小平顶晰磨机备有一套自动测量装置和自动调整机构。在琦磨加工中, 气动测量装置不间断的对加工工件的上、中、下三点进行测量, 且把测量到的数值与规定值相比较, 然后通过电子模拟行程控制装置, 控制琦磨头上下往复运动的的行程, 以及琦磨头两端停留的时间, 因而可保证加工孔的几何精度。当工件达到加工尺寸时, 可自动停止晰磨加工, 从而尺寸精度也得到了保证。小平顶琦磨机目前国内尚不能制造, 我厂的布磨机是由联邦德国N A G E L 公司提供的。
( 4 ) 特殊性加工工序的特点曲轴孔和凸轮轴孔都是细长的间断孔,精变要求比较高, 特别是曲轴孔, 它是由缸体本体与瓦盖组合而形成的, , 加工很复杂,工艺上也很有特点。目前对曲轴孔的加工,国内外有两种不同的工艺安排:
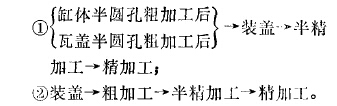
我们采用了前者, 因为半回孔的预加工可一切除大部分的毛坯余量, 在装盖前有足够的时间释放出粗加工中产生的热量, 从而可减少装盖后的热变形及由切削而产生的残余应力。缸体上曲轴孔的半圆孔部分加工的方法很多, 有拉削、锉削、仿形铣削、用球形铣刀铣削等方法。我厂原工艺是半圆孔与顶、底面、主轴承结合面由大拉床一次拉削而成。同平面加工一样, 对半圆孔的加工我厂现在也采用了铣削。目前国外采用球形铣刀铣削半圆孔的比较多, 据说它有机床布局灵活、刀具耐用度高等优点, 但刀具制造难度大; 现在我厂还不能解决。
在调试阶段, 我厂仍旧采用锉削, 此方法虽然比较可靠, 但刀具磨损较快, 待以后条件成熟时, 准备采用一种与锉铣相近的铣削, 在刀具的心轴上, 安装7把铣刀, 刀具的心轴安装在专用的滑座式铣头上, 铣头再安装在侧置式的滑台上, 首先由铣头对着半圆孔与半圆孔之间的空间径向快进, 到位后, 滑台作与半圆孔轴线相平行的工进, 以进行切削。对曲轴轴承端面及瓦片槽的加工, 仍采用了我厂传统的铣削加工方法, 在一根刀具心轴上安装多把三面刃铣刀, 铣刀之间用轴套隔开, 这种加工方法, 刀具更换比较困难,为此最好采用不重磨刀片。这种加工方法振动很大, 因此相邻的两把铣刀的键槽要错开“ 左右, 使刀齿不同时进行切削。另外, 为了加强机床的刚性, 专门设计了超标准的机械滑台, 滑台宽l m , 主轴箱与滑台体设计为一体的, 这样结构刚性好, 主轴箱上设有插销, 夹具上设有相应的导套, 在加工时主轴箱与夹具连成了一体, 加强了机床整个系统的刚性。由于采取了上述措施, 加工时产生的振动减小了, 使加工条件得到了改善。主轴承孔的加工精度不仅取决于机加工水平, 而且与瓦盖的装配质量也有着重要的关系。
在合盖前, 采用了专用多工位清洗机对螺栓孔进行了清洗, 并对大孔内的毛刺和铁屑进行了清除。合盖时, 我们采用了精度很高的扭矩搬手按照一定的技术要求拧紧螺栓, 拧紧时, 扭矩误差可控制在士30 N·m 以内。
为了确保主轴承孔与凸轮轴孔、惰轮孔、定位销孔、水泵孔、油泵孔的位置精度, 以及主轴承孔与止推面的垂直度, 我们把这些孔的半精加工、精加工以及主油道孔的精铰组合在一条自动线内, 实现了孔系的多轴加工, 既保证了加工精度又提高了生产率。此线是从国外引进的, 为了减少机床台数, 在加工孔的安排上过于密集, 因而造成有些主轴之间和导向套之间的间隔过于紧张, 对其强度和刚度将会有些影响。主轴承孔和凸轮轴孔是间断的长孔, 为了提高刀杆的刚度, 采用了多导向加工,即除了前后导向外, 中间也设有导向套。
在半精加工时, 采用滚珠轴承导向套。精加工时, 采用了单列向心推力球轴承的导向套,此轴承通过预紧的办法, 可消除轴向和径向游隙, 从而使运转精度和刚度都比较好。凸轮轴孔中间的导向套, 因空间限制, 采用了滑动轴承。
由于锐杆与导套间存在着间隙, 在熏力作用下锐杆与导套的接触线处在导套的母线上, 当在进行空运转或切削力很小的精加时, 幢杆与导套内孔的接触部位相继发生变化, 导杆与导套的不圆度对加工孔的不圆度影响很大, 而导向装置与锉杆的配合间隙则主要影响加工孔的位置精度。为了保证主轴承孔精度和光沽度的加工稳定性, 美国康明斯公司最后还安排了超精加工工序。所谓超精加工, 实际上就是铰孔, 只不过因为是加工间断的长孔, 除了两端有导向外, 中间也设有导向套, 由于铰刀的精度要求较高, 制造上还有一定难度, 所以超精加工在工艺上虽有安排, 但至今还未能实施。
( 5 ) 其它加工工序的几个特点
由于水泵孔和油泵孔都在缸体上, 因此还要增加一般缸体加工所没有的特定工序,如扩孔、撞孔、惚锥面及平面加工和车槽等,所有这些加工都和两端面其它孔的加工组合在一起进行。此外还有压堵盖和油道、水套泄漏试验等等, 这些工序和传统的方法没有很大区别, 在此就不赘述了。为了提高加工后工件的清洁度, 在工序中安排了两台多工位清洗机。多工位清洗机有清洗、漂洗和吹干三个工位。在清洗、漂洗工位, 工件可翻转三个位置, 以保证工件各个部位都能清洗到。对曲轴孔、凸轮轴孔则采用了探针式喷嘴, 可伸入到孔中进行清洗。而主油道孔因为孔径太小, 不适宜采用探针式喷嘴, 是由专用的喷头贴近工件来进行清洗的。
|