摘要:井下牵引器扶正机构扶正臂的弹性系数与其结构参数密切相关, 在设计时需进行优化。现有文献中采用的方法侧重于选定设计时的参数验算, 不适用于优化设计阶段。鉴于此, 采用“伪刚体模型” 法, 将井下牵引器扶正机构扶正臂的非线性几何变形的分析转化为利用刚体机构理论来求解, 避免了对非线性弹簧函数进行复杂的微积分运算, 用虚功原理分析井下牵引器扶正机构扶正臂的受力、变形及结构参数之间的关系, 建立了力学模型, 得到在扶正臂长度及曲率半径不变的情况下, 随着横截面高度的增加, 扶正臂工作在正常管径和缩颈区域最大应力值的变化幅度随之增加的结论, 优选出适用于150 mm 管径的井下牵引器扶正机构扶正臂的结构参数。研究内容提供了一种对非线性大变形机构进行优化设计的简单方法。
关键词: 井下牵引器; 扶正臂; 非线性变形; 伪刚体模型; 优化设计
0引言
随着钻井技术的发展, 井下牵引器在测井和修井等井下作业领域得到了广泛应用。受工况条件限制,井下牵引器的胀闸、伸缩和扶正等主要结构以串联方式连接, 其径向尺寸远小于轴向尺寸[1-2],在运动和工作过程中, 易发生弯曲变形。因此采用弹性元件作为扶正机构的扶正臂, 依靠其弹性变形实现扶正作用, 同时对机器人的运动进行定位和支撑[3-5] 。
井下牵引器扶正机构扶正臂的弹性系数与其结构参数密切相关, 在设计时需进行优化。一般地,解决此类柔性机构的结构参数设计、受力与变形等问题通常采用椭圆积分和非线性有限元法[6-7] 。陈智等[8] 采用平面曲杆受力与变形模型结合ANSYS有限元分析软件对弓形弹簧进行了分析。艾池等[9] 利用卡氏定理和莫尔定理对弹性限位扶正器的扶正力和位移做了分析, 计算结果在小变形条件下比较理想, 没有分析弹性杆件的大变形情况。这些方法侧重于选定设计时的参数验算, 不适用于优化设计阶段。笔者采用“伪刚体模型” 法[10] 进行研究, 利用刚性构件的位移和转角来近似替代柔性部件的变形, 避免了对非线性弹簧函数进行复杂的微积分运算, 结合虚功原理, 分析扶正臂受力、变形及结构参数之间的关系, 对其结构参数进行优化设计。笔者的研究为分析、设计非线性大变形弹性机构提供了一种简单的解决方法。
1.扶正臂构型分析
图1 所示为井下牵引器结构简图。牵引器由2个胀闸机构、2 个扶正机构和1 个关节机构串联组成, 每个扶正机构具有4 条沿圆周方向对称布置的扶正臂, 支撑牵引器使其位于油管轴线附近。
图1井下牵引器结构简图
井下牵引器进入管道以后, 扶正臂受到管道内壁压迫产生弹性变形。取1 条扶正臂作为分析对象, 设A、B 为扶正臂两端铰接点, A 端固定铰支,B 端为活动铰支可在AB 连线方向运动。以A 点为原点, —A—B—为x 轴, 建立直角坐标系, 受力变形情况见图2。图中: D 为油管内壁直径, mm; d 为扶正臂铰支座直径, mm: w、h 为扶正臂横截面的宽度及高度, mm; R0、R 为扶正臂初始及受力变形后的半径, mm; a0 为端面初始距离, mm; a 为变形后端点距离, mm; b0、b 分别为扶正臂初始与受力变形后弧的高度, mm; θ0、θ 分别为扶正臂端部初始和受力后的变形角, rad; l 为扶正臂长度, mm。
图2 扶正臂受力变形简图
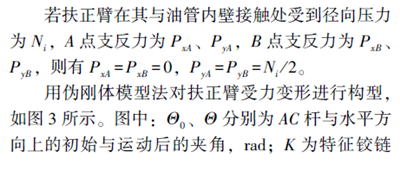
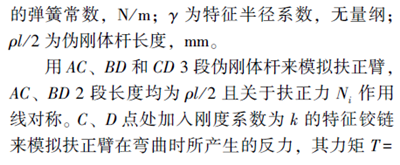
图3 扶正臂的伪刚体构型示意图
2.扶正臂伪刚体构型的扶正力方程
2.1 扶正臂变形与扶正力关系
根据虚功原理, 扶正臂处于平衡状态时, 总虚功为0, 则有:
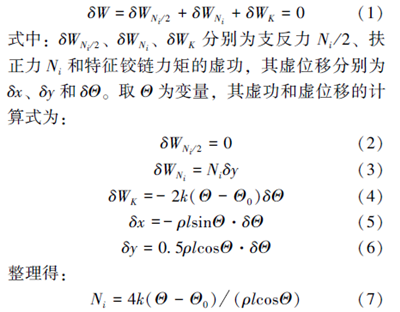
2.2参数解构
如图2 所示, 根据Bernoulli-Euler 方程1/ R0 =dθ / ds, 有2R0θ0 = l, 求得扶正臂B 端在水平和垂直方向上的初始位置表达式为:
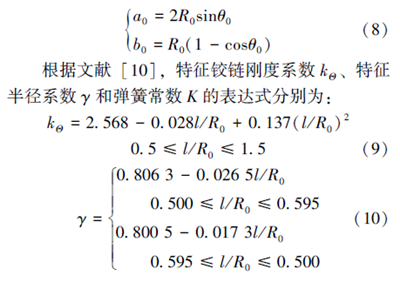
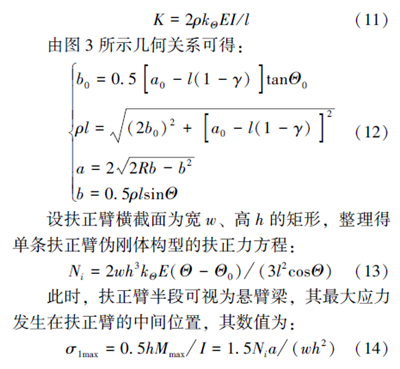
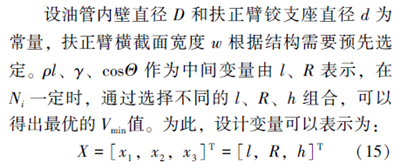
3.2建立目标函数
由式(13),得目标函数表达式为:
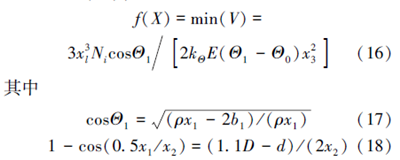
3.3约束条件
3.3.1几何约束
根据井下牵引器结构设计要求, 扶正机构轴向长度L∈ [200, 600], 单位为mm。因此, 扶正臂变形后两端铰接点的轴向距离a 应满足条件: a.(200, 600), 即有:

扶正臂的曲率大于0 且弧长大于管道内径, 其2 倍弦高与铰支座直径之和应当大于管道内径, 于是有:
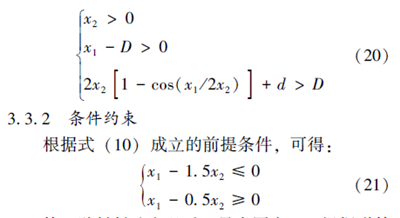
扶正臂材料选定以后, 最大厚度Hmax根据弹簧钢材在油中能淬透的最大厚度确定。设扶正臂材料为60Si2MnA, 则材料在油中能够淬透的最大厚度[11] Hmax =25 mm。
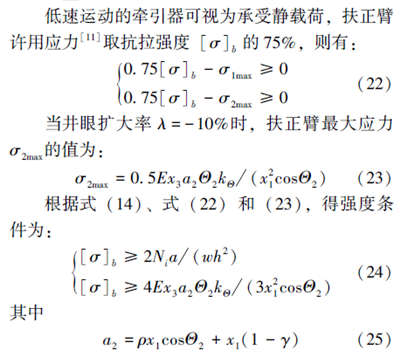
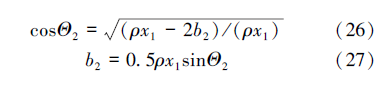
4.算例
4.1优化计算
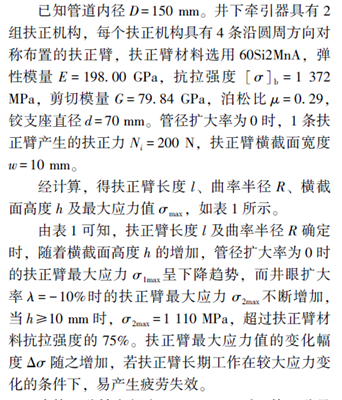
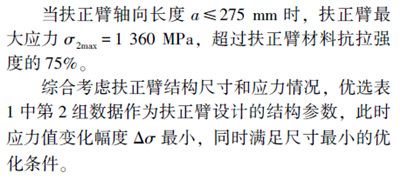
表1扶正臂结构参数组合及应力计算
4.2水平管道爬行扶正力测量试验
扶正机构试验台如图4 所示。井下牵引器安装2 个扶正机构, 每个扶正机构有4 条扶正臂, 扶正臂的结构尺寸由前述优化计算确定。将牵引器置于地面水平管道内爬行, 用拉力传感器测量牵引器通过管道时扶正机构与管道内壁之间的摩擦力。
1、3—扶正机构; 2—井下牵引器; 4—拉力传感器;5—绞车;6—试验台底座。
图4 扶正机构试验台
利用绞车拉动井下牵引器, 旋转绞车调节螺母调节刹带与绞车间的摩擦力, 记录拉力传感器显示的数据。测得扶正机构与管道内壁之间的摩擦力F=300 N, 见表2。
表2 井下牵引器扶正力试验数据
设1条扶正臂产生的扶正力为N, 扶正臂与管道内壁之间的摩擦因数μ =0.15, 则牵引器扶正机构与管道内壁产生的摩擦力之和F = 8Nμ = 1. 2(N)。根据表2 中的试验数据, 得最大摩擦力时扶正臂产生的扶正力N =F / 1.2=245 (N)。与优化设计时的预设条件扶正力Ni = 200 N 相比, 较为接近。存在误差的原因在于管道内壁较为粗糙, 与扶正臂之间的摩擦因数要大于0.15。
5.结论
(1)建立了井下牵引器扶正机构扶正臂的伪刚体模型并进行优化求解, 得到在扶正臂长度及曲率半径不变的情况下, 随着横截面高度的增加, 扶正臂工作在正常管径和缩颈区域最大应力值的变化幅度随之增加的结论, 优选出适用于150 mm 管径的井下牵引器扶正机构扶正臂的结构参数。
(2) 推导出扶正臂的优化设计模型及求解方法, 在确定扶正臂受力与变形之间的关系时, 避免了对非线性弹簧函数进行复杂的微积分运算, 建模和计算比较简单, 适合在精度要求不高的条件下使用。研究内容为分析和设计非线性大变形机构提供了一种简单的解决方法。
(3) 试验结果表明了模型的正确性, 对类似的井下牵引器扶正机构及油田广泛使用的弓形弹簧套管扶正器的设计具有一定的参考价值。
|