随着工业现场测量和质量控制需求的增多,多种用于现场的测量工具应运而生,如激光跟踪仪、关节臂测量机、大型扫描仪等。这类设备相对于传统三坐标而言,精度低且测量过程需要人手动操作,但是可以方便地移动到车间的测量工件附近,无需特殊的温度、湿度、气源等条件,在车间环境中也可以保证测量精度。因具备便携性和方便性,这类设备得到了广泛的应用。其中,激光跟踪仪以其适合于汽车车身测量的方便性、量程和精度,在车身主机厂、配套厂得到认可,作为三坐标测量设备的补充,越来越多地出现在车间的测量现场。 激光跟踪仪6D测量技术
传统的激光跟踪仪测量以3D测量为主,即反射镜(靶镜)测量方式,测量的数值为球心坐标值X,Y,Z(也可以以其他坐标系方式显示),主要应用于航空航天、汽车中工装、型架等部件的测量、安装和调整。随着工业领域应用需求的增多,除了单一的通过反射镜进行测量和跟踪,使用者更希望将跟踪仪应用到加工工件的测量中。这类工件形状复杂,测量特征分布广泛,单纯依靠跟踪仪转站和隐藏点辅助测量工具已经很难满足精度和效率的测量要求。
在这种情况下,Leica的6D测量产品——T系列解决方案应运而生。T系列测量工具的原理是通过在跟踪仪上增加T-Cam相机,从而在测量和跟踪过程中,不仅可以监控跟踪目标的X,Y,Z(中心值),同时还可以提取目标的 I,J,K(沿三个方向的扭转)用于代表目标的旋转姿态。这种方式可以得到更多的计算信息(见图1)。
⒈ 走动式三坐标——T-Probe测头
通过在T-Probe测头上增加红宝石探针,可以使其像三坐标测量机一样完成工件上的接触测量,测量范围能够达到直径50m。这样既方便地利用了激光跟踪仪的现场适应能力、便携性能,又能够满足车身工件的高精度测量需求,可应用于车身零部件、分总成、匹配等过程中的检测和问题诊断。
在使用过程中,测头无线连接任何电缆,本身自带锂电池,通过点击测量工具上的按键可以进行测量、删除、连续扫描等操作,从而将激光跟踪仪扩展成为走动式的三坐标测量系统,真正实现无线、无臂操作(见图2)。
⒉ 非接触测量——T-Scan测头
除T-Probe之外,T系列工具还同时包括可以满足大尺寸空间扫描需求的T-Scan系统(见图3)。使用人员可以通过手持T-scan测头,以点云、三角网格、曲面渲染等多种方式反映工件的表面形状信息,用于曲面形状比对分析、尺寸控制、逆向等。 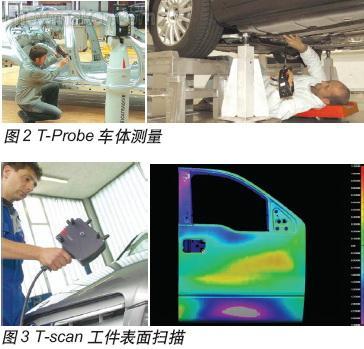 相对于硬测头单点测量,T-scan测量效率更高,测头每秒可以测量20000个点,应用于车身轮廓扫描对比检测、逆向、Flush&Gap分析、腰线测量等。
车身检测中的6D测量技术应用
⒈ 车身关键特征尺寸测量
在车身中,有大量的特征点、固定孔、槽、圆柱等特征需要进行快速检测,特别是车身内部的安装孔位,需要测量设备在保证精度的前提下能够方便地进入测量。T-Probe无线、无臂的特点正满足了这种需求。T-Probe整个系统空间测量精度能够达到7um/m,通过不同探针长度及安装位置的组合,可以实现车身特征的全尺寸检测,且测头操作方式友好,单人就可以完成测量。
⒉ 车身覆盖件曲面扫描
随着汽车制造业的发展,对车身覆盖件的曲面轮廓质量的控制越来越重要。传统车身轮廓检测以接触方式进行单点采集或连续扫描为主,将获取的单点的坐标和理论点坐标相比,在车身表面以抽样的方式进行曲面轮廓对比。
近年来,Leica T-Scan激光扫描测头以其快速的点云采集得到了越来越广泛的应用。其主要特点如下:
* 快速的点云采集速度,20000点/秒;
* 工件三维轮廓的实时显示;
* 点数据与CAD软件的通用性;
* 快速直观的比对色差输出;
* 坐标系可以根据测量需求灵活调整,指导工件制造过程;
* 数据采集后,可以随时进行调用分析,具有可追朔性;
* 能适应不同颜色、不同反光表面的工件,测量无需喷粉 。
其一般的检测过程如下(见图4、图5):
⒊ 车身配合尺寸分析
在汽车制造过程中,除了要保证车身各零部件、分总成满足尺寸控制公差外,还要确保经过焊接、铰链、胶合等方式组装后各部件之间的相互关系满足要求,如前盖和翼子板、车灯和侧围、车门之间、天窗和车顶盖等。这些尺寸控制直接影响车身的外观、使用稳定性以及功能型要求。在这类使用中,可以采用T-Probe(完成关键位置快速测量)和T-Scan(间隙轮廓全面分析)相结合的方式(见图6、图7、图8)。
综上可知,Leica激光跟踪仪的T-Probe和T-Scan 6D测量附件以其良好的车间现场适应性、手动操作方便性及便携性能,可以快速完成车间现场车身零件检测、匹配分析、安装调整等任务,在车身测量中具有很大的应用价值。
|